The Client
Carlsberg has grown to be one of the largest beer brewers in the UK having began brewing in Denmark in 1847. The company now supplies 140 countries worldwide and was responsible for brewing Denmark’s first beer with a type of yeast from which almost all modern-day lagers are derived. Its bottling plant in Northampton produces 54,000 bottles of beer an hour.
The Challenge
To meet changing health and safety legislation relating to exposure to noise in the workplace, the plant required an acoustic solution to address the noise level produced in a few areas around the bottling line which was impacting on operational staff working within these areas. A separate requirement was to deliver a fully air-conditioned noise haven to be used as a shift manager’s office.
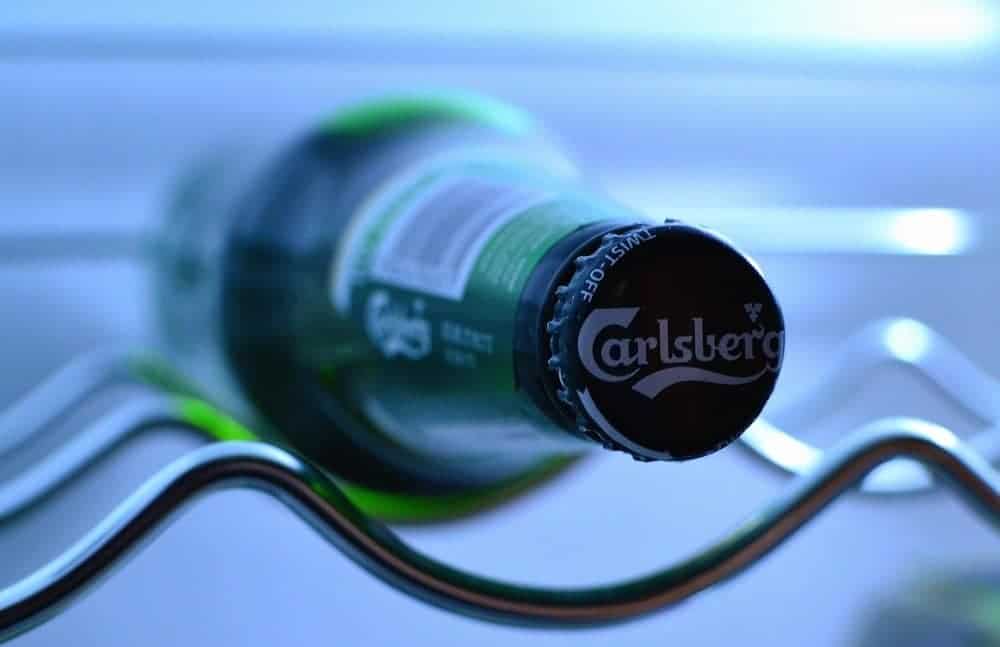
The Solution
Kimpton Acoustics was appointed to undertake three installations across the plant to meet the specified health and safety regulations. Bottle line conveyors are characteristically noisy over the distance they travel to the filling station, therefore acoustic canopies were installed to reduce noise levels, whilst ensuring total visibility and multiple access points along the full length of the conveyor.
Fully air-conditioned noise havens are becoming increasingly popular in automated plant areas and just such an area was created for use as a shift managers office as part of the scheme.
To reduce the noise level at source, and therefore provide a quiet environment for machine operators standing adjacent to the equipment, Kimpton installed acoustic enclosures on the rinser infeed, labeller infeeds and Wrapround infeed.
The design, manufacture and installation of the noise management solutions were completed within budget and with minimal disruption to the daily activity of the plant.