We have recently completed the installation of an acoustic enclosure range for Ardagh Group, formerly Ball Packaging Europe, based on Deeside. They operate a huge production facility for aluminium can production. Worldwide, Ardagh operate 109 facilities in 22 countries with over €7.6 billion in global sales.
The Deeside factory produces the top section for drinks cans. Ardagh Group are making a major investment in the new press machinery to deliver a refreshed can top design in response to the changing demands of customers. As you can imagine, the industrial pressing and forming of aluminium can tops is not a quiet business.
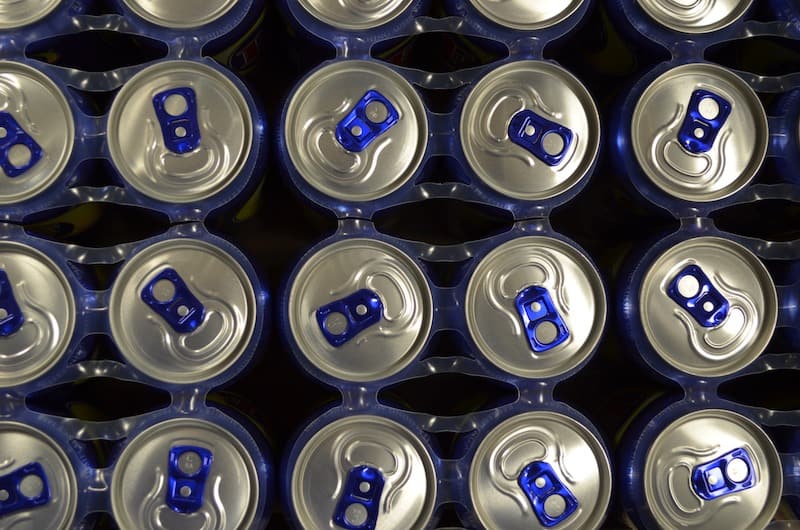
Under The Control of Noise at Work Regulations 2005 any employer has a legal responsibility to protect their workers from the risks caused by noise. Hearing damage caused by exposure to noise at work is permanent, incurable and a definite risk to employers unaware of their responsibilities. Research estimates that over 2 million people are exposed to noise levels at work that may be harmful. It’s also interesting that according to the Health and Safety Executive (HSE), hearing loss is usually gradual, due to prolonged exposure to noise. It may only be when damage caused by noise over the years combines with normal hearing loss due to aging, that people realise how badly their hearing has been affected.
Our role has been to design, manufacture and install acoustic enclosures for the presses to ensure personnel within the factory are protected, as well as to control nuisance noise affecting neighbours. At the first action level (80dB) employers must provide information and training, and make hearing protection available, which is already in place in the factory. However, the weekly average limit of 85dB which is the second action level advised by the HSE is well below the noise of the end presses in this plant – so engineering controls were essential.
Keeping production going in the factory while these major upgrade works were undertaken was a challenge for the production engineers and required a great deal of commitment by all involved to ensure the installations were completed safely and with the least disruption possible to production. Shutdown work is always a challenge that comes with tight timescales and requires a dedicated team that works collaboratively to a plan, while maintaining a willingness and flexibility to resolve any unforeseen issues promptly in order to ensure the success of the project. Whilst installing an acoustic enclosure may be our priority, continuing to meet production schedules is most definitely there’s, so we have to work fast and carefully.
Aluminium can production is one of those industrial operations that is quite mesmerising as the speed they are formed is breath-taking. The multi-stage process to draw the body of the can itself can be completed in under a second. The side walls of a can are only 75 microns thick, so there is an almost delicate nature to handling them too. In the Deeside plant, it is the lids that are made , and it is only at their customer’s factory that they are mated with the can body and sealed – once it has been filled with the drink ready for sale.
It’s a process most of us would probably take for granted, but adding the top to the can lid not only has to happen fast for economic production, but also very precisely for the beverage end to work reliably. This means machines have to be set up carefully and every part of the jigsaw has to do its job perfectly. It’s with all of these constraints our team set about designing the enclosures for the presses in 3D, working around all manner of conveyors, pipework, cabling, gantries etc as well as the machines themselves to ensure each enclosure not only performed acoustically but also provided the supporting structure for the equipment – with openings in just the right place and all the steelwork threading through this forest of equipment. We do love a challenge.
If you’d like to see in more detail about aluminium can production, this brilliant video explains the process perfectly.